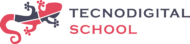
Showcasing simulation of composite materials with Abaqus
These are some of the models that I have developed using Abaqus and the automation capabilities of Python scripting.
Transverse cracking of cross-ply laminates
The aim of this work was to study the appearance of transverse cracks in cross-ply laminates, i.e. laminates made of unidirectional plies with a [0/90/0] layup, under tensile loading. A computational micromechanics approach (CMM) was employed to capture the cracking mechanism of the 90-ply in detail. Since the length of the model was relatively large for a CMM simulation, the 2D plane strain hypothesis was required to keep the computational cost within feasible limits. CMM models often involve an important geometrical complexity because of the enormous number of fibers that are usually represented. In this case, with a carbon fiber volume fraction around 65%, ply thickness up to 280 um and 10 mm of length, the number of fibers went above 28000 fibers! No need to say that creating these models is only possible using Abaqus Scripting with Python, and still it took a few hours to completely generate the partitions of the fibers, the partitions of the fiber-matrix interfaces, and meshing the whole part.
The results showed beautiful cracking patterns that reached saturation when the spacing between adjacent cracks was close to the thickness of the 90-ply. Stress relaxation was observed around the cracked regions as expected, because of the new free surfaces generated.
Computing the average stress sustained by the 90-ply was also possible thanks to automating, with a Python script, the computation of the average stress sustained by all of the finite elements of this ply in the loading direction (σ₁₁). It may sound straight forward to get the average, but it was a weighted average with the elements size, which was computed based on the coordinates of the nodes of each element in the same Python script!
Using CMM presents some advantages, such as the great detail that can be achieved by explicitly representing the constituents of the composite material: matrix (polymer resin), reinforcement (continuous fibers) and interface (fiber-matrix bonding). On the other hand, the generation of these models (e.g. geometry and mesh) is only possible by means of automated tools, such as Python scripts in the case of Abaqus.
More details here:
M. Herráez, D. Mora, F. Naya, C.S. Lopes, C. González, J. LLorca, Transverse cracking of cross-ply laminates: A computational micromechanics perspective, Compos. Sci. Technol. 110 (2015) 196–204.